4-Axis CNC Mill Restoration
Fadal VMC
The Fadal is the only mill with a 4th axis turntable in our machine shop. It dates back to the 90’s and uses technology from even earlier. Historically the Penn Electric Racing team has been the only on-campus organization with the need for the machine, and has had sole responsibility for its upkeep without support from shop staff.
Unfortunately, in the past year or two it encountered a seemingly fatal error and the team was unable to continue working on it. The select few who knew how to operate it had graduated without properly teaching a new member or creating thorough documentation. I embarked on the journey of getting it fully operational, starting essentially from scratch facing an error code I knew nothing about on a machine I didn’t know how to operate.
With my background knowledge using other CNC mills and the help of one recent graduate I was still in contact with, I went through the debugging process. I read countless online forums and pages from the manuals and eventually fixed each successive error, learning how to operate the machine along the way. In the end the machine was back to its former glory and I was able to produce a few parts, write a new condensed operation guide for future users, and even test the 4th axis before the COVID-19 quarantine shut everything down.
Debugging
The machine had one critical error preventing it from operating: an amplifier fault on the Z-axis. As it turns out, there’s a variety of different things that could cause this fault and a plethora of potential fixes. After reading up on as much info online and in the user manual, I was able to narrow down the problem to the Z-axis amplifier board. After digging up some old emails on previous repairs, we luckily found that we already had the exact replacement board on hand. After this breakthrough, I began teaching myself how to operate the machine from the manual, figuring out the software for generating G-code and uploading it to the machine, and finally ensuring that the machine was doing what the CAM software was intending it to do.
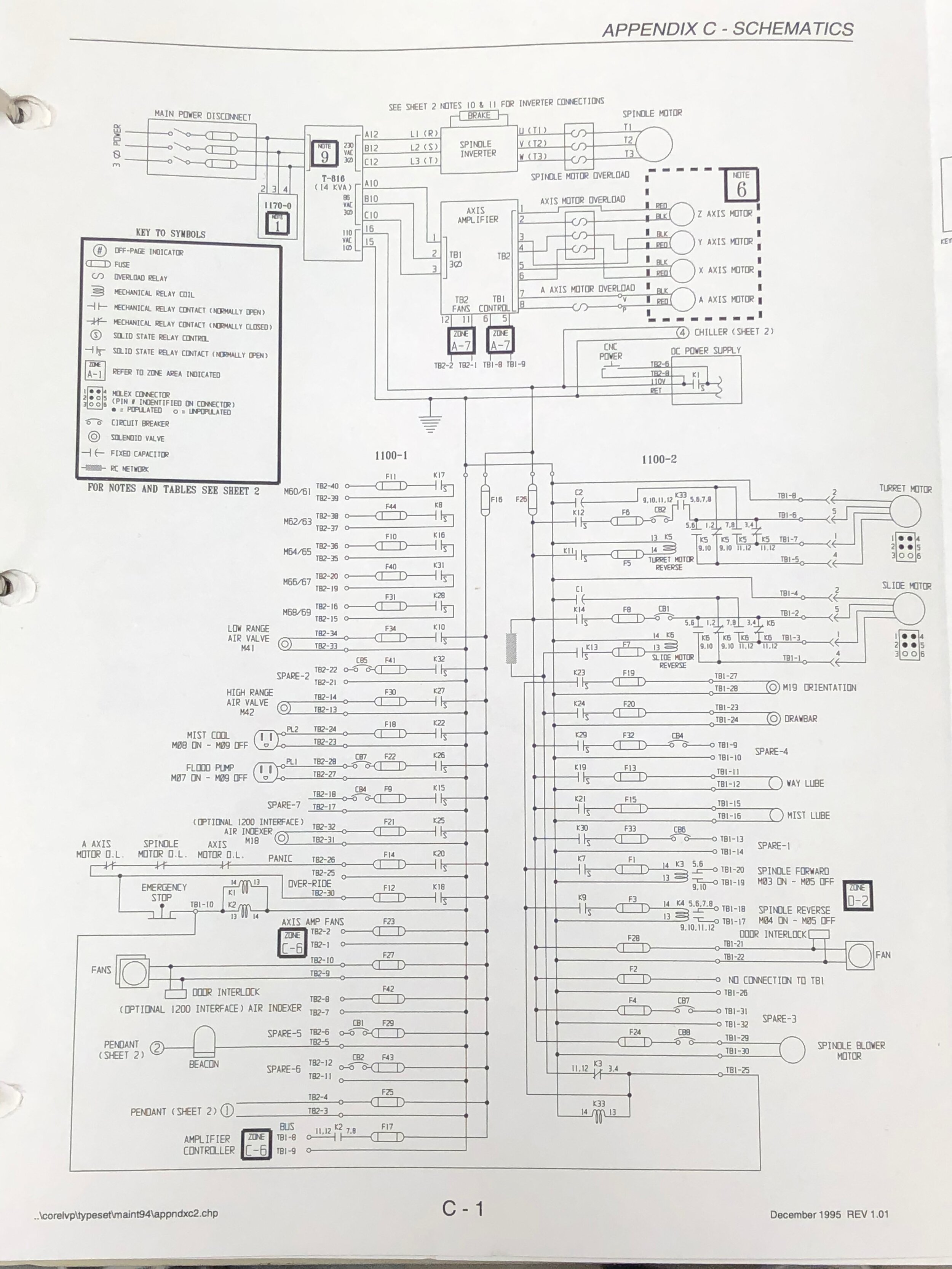
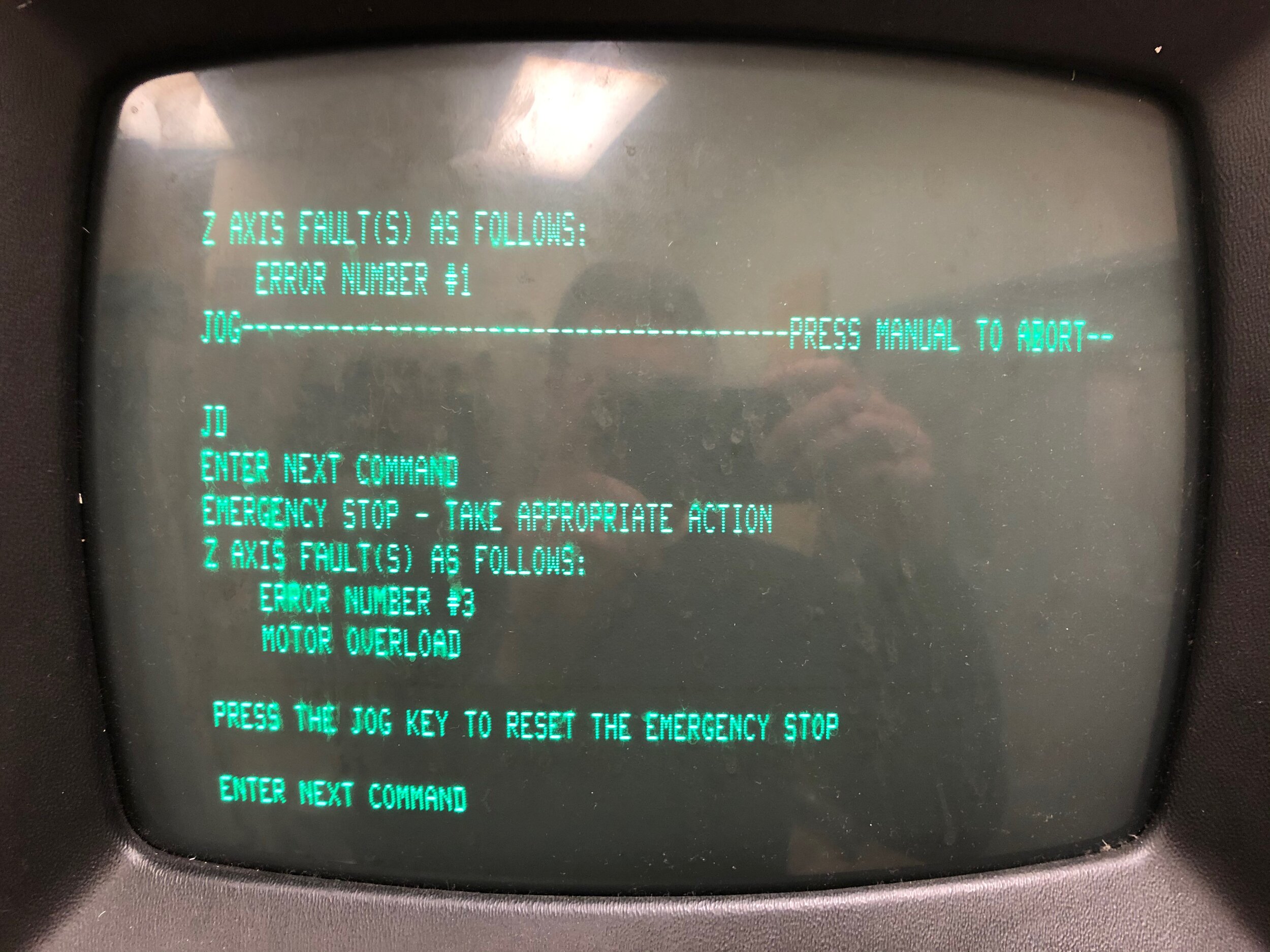
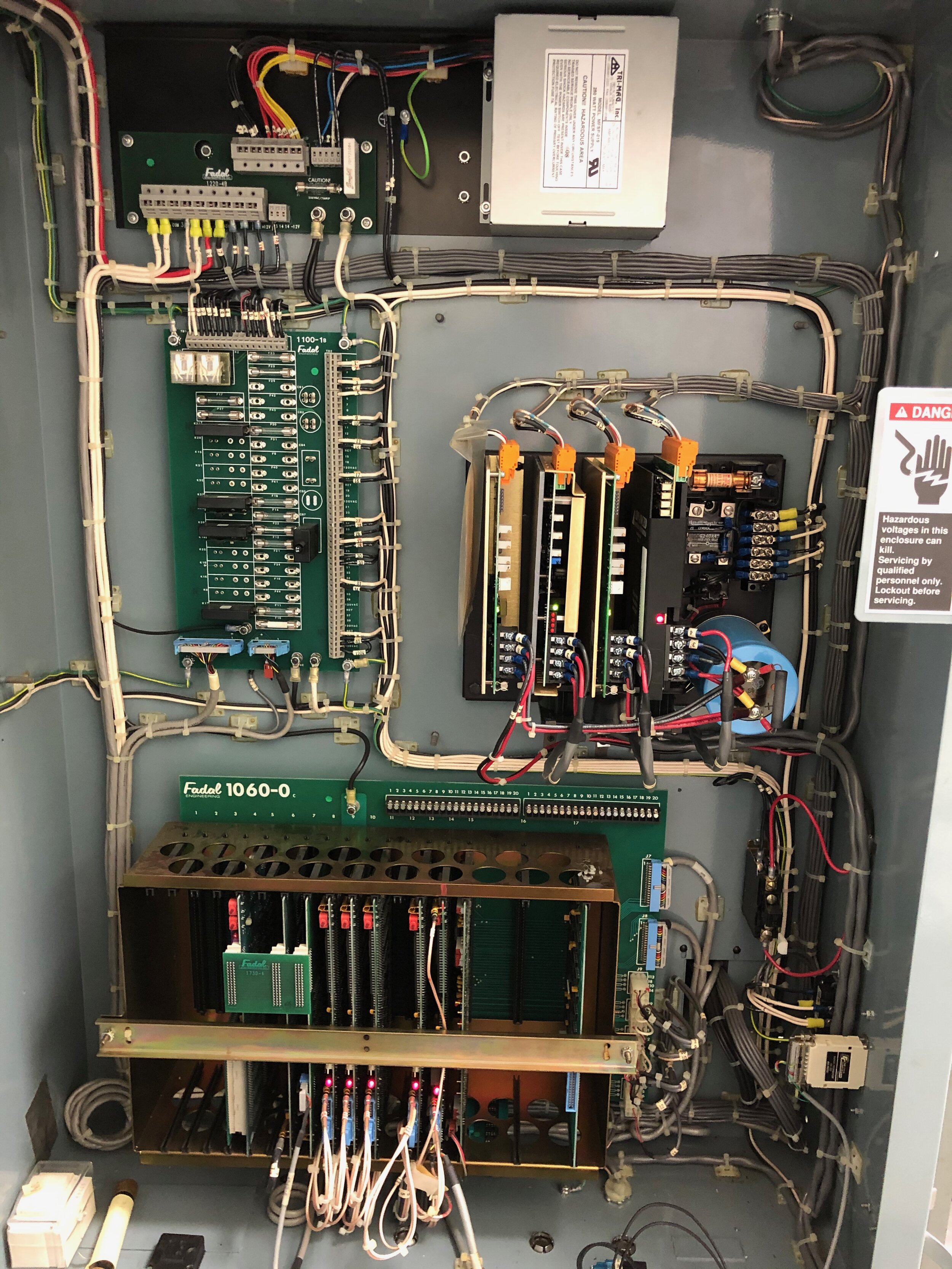

Coolant
Having not been replaced for over a year, the coolant had completely evaporated leaving a crude oily concentrate. After a full days cleaning by hand and flushing the system with a cleaning solution, the coolant was ready for use.

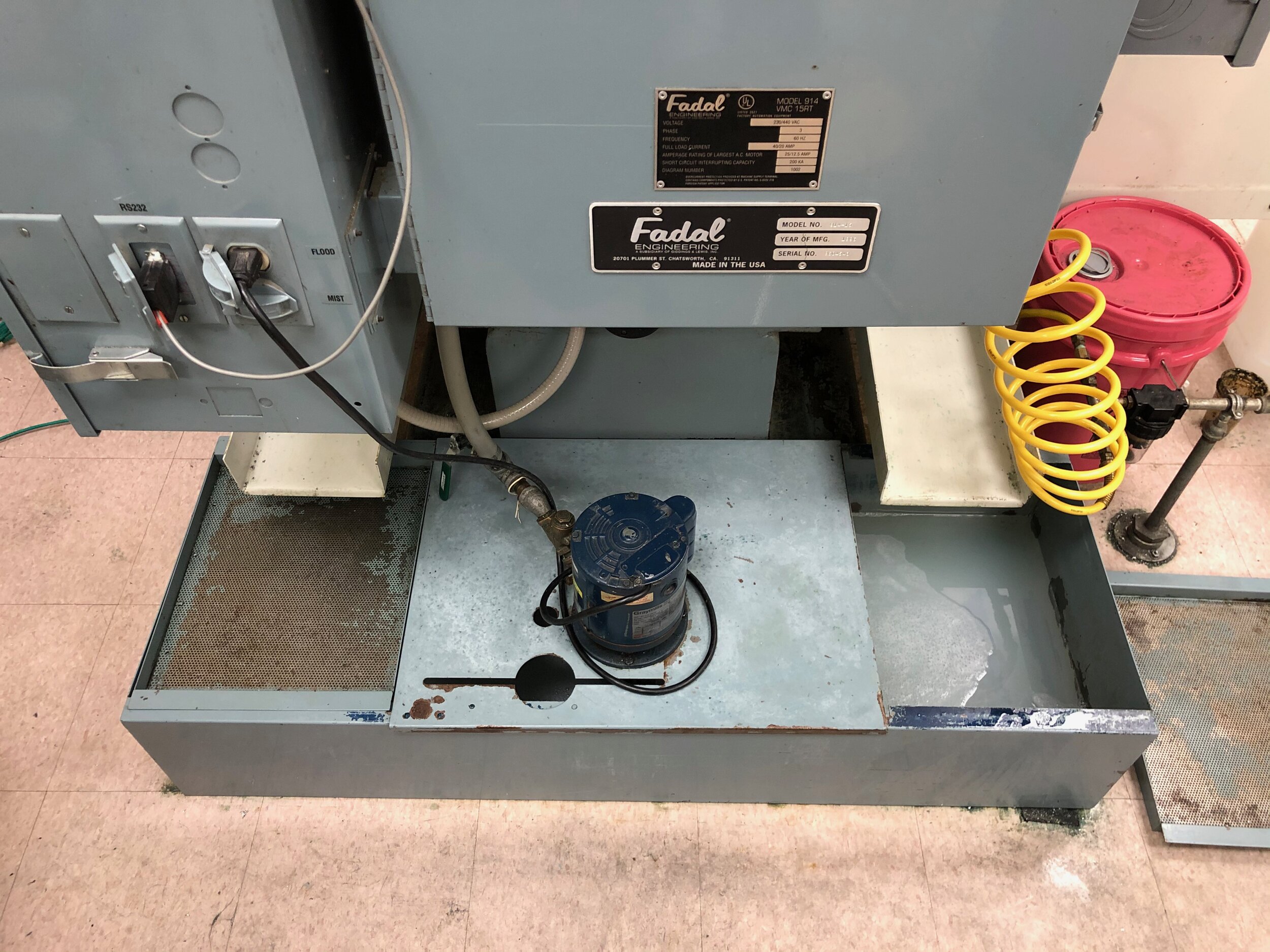
Tool Holders
Another fact of life is corrosion, which was luckily not hard to counteract with some scotch brite and WD-40. With regular procedure now to include wiping down the tool holders to knock off any rust, they were ready for use.
Suspension Bearing Mounts
These parts each needed to be pre-drilled, reamed, and chamfered with high precision for spherical bearing swaging to be used as the rod ends in an FSAE car’s suspension. A production run of 34 parts with all the same operations using three different tools is a perfect test for a CNC machine. Using G-code from MasterCAM and fixtures allowing for locating using a tool in the spindle, it was as easy as screwing two bolts and pressing go. After that, the machine does the rest with automatic tool change and coolant. There’s probably better and more efficient ways of fixturing, but given our timeline and relatively low quantity this got the job done.
Pedal Box Beam
With lots of irregular geometries to mill out for weight reduction, this part is another good candidate for a CNC mill. We also wanted to test an automatic chamfering operation which would essentially deburr the part, however the CAM wouldn't cooperate so we had to do it by hand. Nonetheless, the automatic tool changing made itself useful with the part using 8 different tools.
4th Axis Test Part
This part was purely an experiment to see if the 4th axis would even work since it hadn't been used in over a year. The easiest setup was with the 3-jaw chuck attachment for the turntable using a piece of round bar stock. I created a few features that would test different CAM features using both positional and continuous 4th axis motion. Not all features worked as expected, which is likely a mismatch between what the code compiler thinks it should do and what the machine is expecting and will ultimately execute. This part was completed a few days before COVID-19 shut down the university, so no further experimentation was possible.